Table of Contents
Optimizing a warehouse does not only mean working on a supply chain or the quickest cargo dispatch. It means working on various factors that simplify and enhance your operation. For instance: Optimizing warehouse storage means examining each corner of a warehouse infrastructure that identifies the correct efficiency to boost the overall workflow of an organization. Maintaining a good warehouse depends on numerous factors such as production process, supply chain, smart layout design, and advanced inventory management techniques. Operating efficiency in your warehouse storage creates a healthier bottom line but also improves a company’s process.
They are implementing the right strategies and advanced technologies such as introducing smart layout designs and advanced inventory management techniques.
In this article, we will explain how smart layouts, warehouse design, and advanced strategies can maximize the entire operation and productivity of a warehouse.
Let’s delve deep into this article to learn the strategies and key aspects of a supply chain to improve your warehouse space efficiently To help you recognize and address advanced components of the warehouse that involve making the warehouse efficient.
Here is a breakdown:
- Smart Layout Design: Warehouse Layout
If you want to make your entire operation of the warehouse run faster, one of the crucial steps is working on the main factor which is layout. Implementing a systematic approach to floor allocation, working on strategies like product velocity, and picking frequency. Efficiently implementing vertical space with tall shelves for huge parcels can utilize space in your warehouse. And placing trending items closer to the packing area for quicker access so that the warehouse operation can run faster.
- Adding Mezzanine above a Floor Level procedure: Storage Space
To improve the efficiency of a warehouse adding a mezzanine is one of the effective ways to expand the storage of a warehouse.
Installing a mezzanine is a floor-level process such as for shipping or receiving room. Unfortunately, there are pitfalls with a mezzanine as well.
- Customized Storage Location: Space Management
Designing a specific place for half-pallet quantities. Free up space within the warehouse layout to accommodate items that are received or packed in half quantity. This approach eliminates the requirement of huge places for items that are received in half quantities. If you condense your pallet you can make more space to put more pallets in the same space without taking a huge portion of space.
- Adjustable/Flexibility in Storage: Improve Your Warehouse
Creating adjustable shelves in a warehouse that can be moved according to the preference of products or space. For instance, flexibility ensures handling partial pallets without wasting space. Moving shelves can eliminate the picking process. You can move the adjustable shelf and put it away wherever you want.
- Use Space Available: Space Utilization
Make use of space you never used before. There is always additional space for products of receiving or shipping doors where pallets that are going to be supplied, slowly moving material, and products inbound or outbound that have not yet been processed can be kept.
- For Seasonal Items Make Use of Trailers: Storage Capacity
Sometimes storing your products in trailers in a warehouse can eliminate a huge space for storage. This can be beneficial for seasonal products, especially among retailers.
- Product Segmentation:
To improve efficiency, categorize the products based on factors such as demand frequency size, weight, and handling requirements.
Keep similar products closer so that they can be picked quickly to facilitate streamlined picking and packing processes.
- Zoning Strategies:
To protect the perishable products placed in the warehouse depending on the nature of products and their movements within the facility. Common work includes picking, packing, and delivering.
- Velocity-Based Slotting: Maximize Warehouse
To enhance the efficiency of the warehouse it is crucial to place items closer to packing and shipping areas to save trip time during order fulfillment.
An item that is not in a hurry to deliver soon can be placed in a remote place to eliminate defiled storage places for other delivering items.
- Make Use of Vertical Space: Warehouse Space Utilization
Install tall shelves for huge parcels that can be placed or a racking system to maximize vertical storage space.
To reduce the need for redundant vertical movement, pick items at accessible heights first.
- Pick Paths and Flow: Optimize Your Warehouse
To reduce the travel time-consuming process it is necessary to create pick paths that reduce the amount of distance from the warehouse.
Create warehouse route metrics and sensible flow to prevent congestion and blockages.
- One Way Traffic: Improve Warehouse
Use only one way for inbound or outbound products to reduce the chances of congestion and collisions between material-handling products. However, placing receiving, and delivering goods closely minimizes the distance goods need to travel within the warehouse. This helps in a faster order fulfillment process.
- Bulk Storage and Selective Racking: Storage System
To protect the finishing of the product choose the best storage option considering the feature and sensitivity of the item.
If you have a lot of the same SKU, reserve bulk storage for large quantities of the same item. Selective working may work well for smaller amounts of different SKUs.
- Required Temperature and Storage Conditions:
When planning a layout it is necessary to consider temperature and storage requirements into consideration. Especially for items that require certain environmental conditions.
Allocate room for items that require storage space for specific temperature controls.
- Automatic Layout Modification: Warehouse Storage Space Utilization
Design a fine layout for carrying products also adaptable to changes in inventory, product lines, or industry requirements. Regulatory layout assessments to enhance the entire supply chain process.
- Safety Consideration in Account:
To protect the life of warehouse workers and protect products kept in the warehouse, ensuring clear pathways, proper signage, and specified areas for tools and pedestrian traffic.
Following safety measures while handling hazardous material or fragile items.
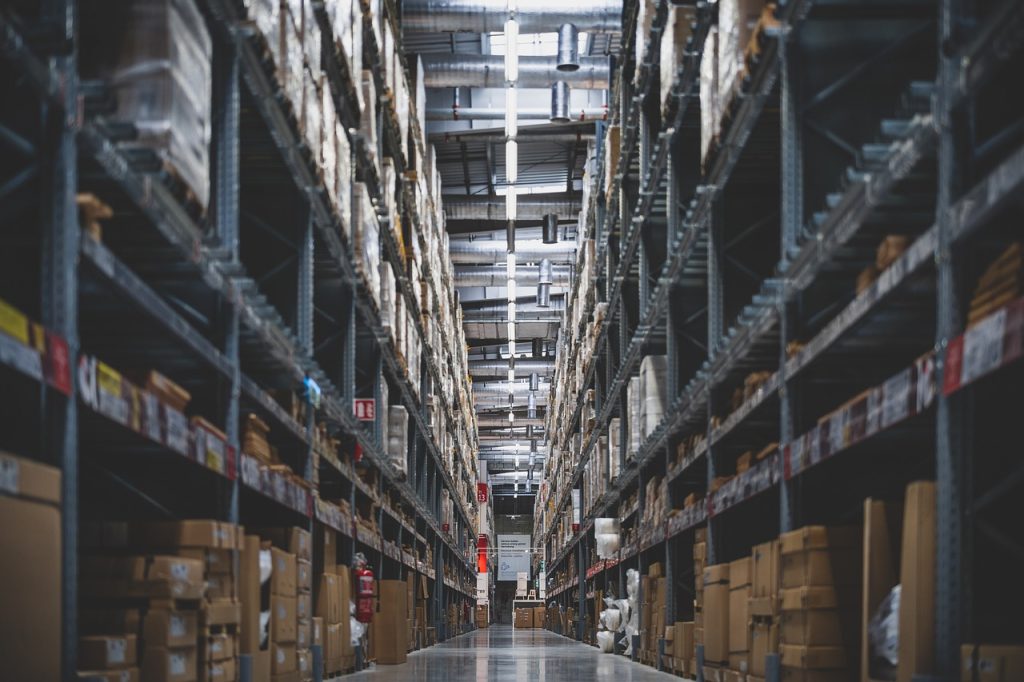
- Enhanced Inventory Management: Optimize the Storage
To run your warehouse supply chain smoothly, integration of art inventory management is mandatory to enhance accuracy and visibility. Implementing automated systems that can track real-time tracking eliminates the risk of stockouts or overstock situations.
Utilize barcoding of RFID technology on parcels for quick and error-free identification of products.
- Real-Time Tracking:
Implement a system that provides real-time visibility into stocklist levels and movements.
Use RFID (Radio Frequency Identification) barcode scanning or similar technologies to monitor things instantly and precisely.
- Market Forecasting:
Keep in account data analytics and the history of records to make informed decisions.
To avoid incidents to prevent stockouts and overstock anticipate trends and adjust inventory levels.
- Automated Reordering:
You can enhance the overall operation of the supply chain by installing restock orders triggering the automatic refilling system when a certain inventory level falls below a predefined point.
Technological systems reduce manual intervention and instantly eliminate human error and the risk of stockouts.
- Batch and Serial Number Tracking:
To maintain the efficiency of supply chain and logistics it is significant to track the serial number and batch code of items. For instance: manufacturing or expiry date.
Improve traceability, make refunds, and facilitate recalls or quantity monitoring measures when necessary.
- Multi-Channel Integration:
Implementing advanced technologies integrating cutting-edge inventory management via various sales. For instance: Online, Offline, etc
Maintain a uniform inventory view to reduce overselling and improve order-fulfillment operations.
Make use of cross-docking strategies and techniques to reduce storage time and accelerate the flow of goods through the warehouse.
Optimize the process of moving goods from one place to another from storage to shipping without unnecessary storage which instantly enhances the warehouse process.
- Dynamic Slotting: Optimization
To improve storage efficiency it is significant to maintain regular reassessments which means placing the items according to their turnover rates and popularity. This will eventually improve the storage operation by identifying trends and optimizing layouts through data analytics.
In addition, the famous methods that have been used by many industries are ABC methods. For instance: categorizing products into 3 groups based on their importance. Group A for High-priority products, Group B for Moderate items, and Group C for Low-priority items. This helps in accessing items quickly in a location.
- Invest in Right Warehouse Efficient Place Utilization:
The crucial step of choosing the right warehouse that fits your storage goods is as important as fulfilling order completion. These steps improve the storage operation efficiency.
The correct method of warehouse storage depends on the product size and the number of products as well as how you manage your entire warehouse.
Here is a breakdown of some wide methods used by the warehouses today:
- Strategic Floor and Block Stacking Technique:
The most effective approach which is widely used in warehouses is floor and block stacking techniques which is also very popular. Because it works well with warehouses that have modest ceiling heights. In block stacking, the items are packed in unit loads and stacked on the floor at the highest safe height.
Mostly durable goods such as refrigerators, canned products, and bottles are stored in this way.
- Strategic Pallet Flow Racking:
For products such as FIFO (first in, First out) stock rotation pallets flow racking can be the optimum choice for warehouses. Pallets are loaded at the apex of slopping lanes and when the item is removed during the picking process gravity pulls the boxes down which effectively saves time and effort.This sort of method leverages the least amount of floor space and needs only two aisles. For a loading and picking face.
- Strategic Push Back Racking:
The method that works best for LIFO ( last in, first out) inventory management is push-back racking as opposed to Pallet flow racking. Advanced technology made work easier through solid steel rails, pallets automatically pushed back when an item is loaded and come forward when it is unloaded.
- Use Containers According to Goods Size:
The approach warehouses use to store a product in a container is a beneficial method but if done incorrectly can make things hectic for you. It is necessary to use the containers according to the goods’ size which will instantly utilize less space and effort. Mainly, warehouses face storage issues because they select the wrong container for goods or use the same container for different products.
To optimize warehouse storage efficiency it is crucial to use containers of various sizes depending on the good sizes. Store small items in small containers and the items in huge containers which will increase the efficiency of warehouse storage.
Upgrading and Enhancing Warehouse Management:
In today’s fast-paced and economically dynamic world optimizing a warehouse can influence your business or can give you positive/negative outcomes depending on what input you have put in. It is crucial to know that Great Power comes with Great Responsibility. What you invest in your business gives you 3x of what it generates. It can be advantageous and sadly time disadvantageous.
This section covers core strategies you can implement to improve warehouse storage efficiencently which will benefit you and your business.
Here is a breakdown:
- Advance Planning:
To run the warehouse can be a crucial task as it takes alot of effort and planning to maintain the efficiency of warehouse storage. It is vital to maintain a balance between forethoughtful planning and making the most of present resources. Therefore, Routine assessment of space utilization is essential, as it provides insights into potential areas for improvements.
The shelving system must be flexible, through systematic adaptation, you can allocate places for high-turnover products ensuring timely packing. While less moving items can be arranged more proactively.
While implementing advanced robots and technologies into supply chain management such as automated systems and retrieval systems. (AS/RS) that further improves the operation improving storage capacity and retrieval times. Thus, technology plays a vital role but thinking of a human is impossible. So it is important to get the opinion of warehouse staff which is invaluable. Their practical expertise and experience may provide insightful observation into the intricacies of space management. Thus, their viewpoints matter.
Also Read: How does Cross docking work?
Advantages of Effective Storage in Warehouse Operation:
Effective storage operation in a warehouse is crucial to maintain the entire business and make it run smoothly. If done correctly it can give various benefits to business.
Let’s explore some of the key benefits:
- Minimizing Holding Cost:
Optimizing warehouse storage operations can enhance the entire process in business. Holding parcels and placing them and utilizing them in different places. Instantly, reduce expenses to warehouse spaces, improve insurance, and overall operation.
- Reduces Stock Risk:
Implementing advanced strategies for warehouse storage can eliminate multiple issues. It also enables better tracking, and monitoring movement of goods while shifting from one place to another. That reduces the risk of theft, damage, or misplacement. This approach eliminates stock losses and improves the entire security in the warehouse.
- Efficient Storage Utilization:
Maintaining the proper storage utilization in warehouses can allow businesses to operate properly. By optimizing storage operation and working it correctly such as racking and shelving. Businesses can utilize storage capacity and improve the entire operation following this approach.
- Future Planning:
Effective optimization storage operations can also facilitate accurate demand forecasting by delivering insights into data analytics. Such as sales data, trends, and improved customer service. This allows businesses to make informed decisions regarding production forecasting, receiving, and dispatching.
- Cost Saving:
Providing timely delivery reduces the storage space and hence eliminates carrying costs, minimizes stock losses, and optimizes storage space. Optimizing warehouse storage control cost saving for industries. This can positively impact business shares and productivity.
- Improve Supply Chain Operation:
Optimization of storage warehouses can improve the entire operation of supply chain activity. That aligns with customers’ demands in distribution and manufacturing, resulting in smoother and reduced delivery times. For instance: satisfying customers’ demands can enhance the supply chain activity and improve customer satisfaction reviews.
- Informed Decision:
Correct information provided by inventory information management can control the system can make data-driven decisions. Based on real updates offering insight businesses can make informed decisions regarding purchasing strategies, real-time techniques, and production planning.
- Enhanced Cooperation:
Sales, buying, and delivering, and other departments within the organization when inventory control is implemented effectively. Clear visibility and information shared can enhance the operation and thus deliver efficient workflow.
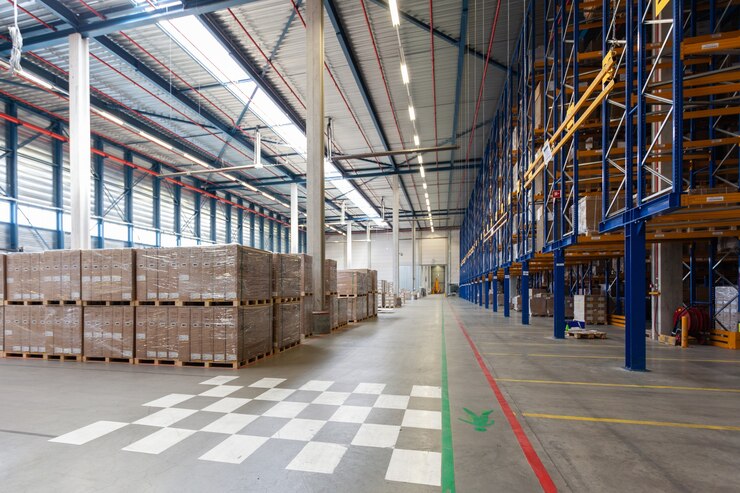
Using Barcode, RFID, and Advanced Technologies to Provide Accurate Training:
This approach plays a huge in a warehouse making use of advanced technologies including barcode and RFID, to track items so that the work can be done faster and smoother eliminating the need to store products that can be dispatched on time. This method is widely used by industries and businesses that have increased their workflow and optimized storage in warehouses.
These technologies and approaches have shown positive results and several benefits in improving supply chain activity.
Here is how Barcode and RFID technology works to reduce the storage space in a warehouse.
Barcode procedure:
- Recording and Gathering Data:
Implementing a barcode system through barcode handles can make work easier by simply scanning goods quickly and smoothly eliminating human error. For up-to-date information, this data can be sent straightaway to the inventory management system which they efficiently keep in the record and start working on further process. This method reduces the time of holding products and saves the time and effort of warehouse employees.
- Individual Identification:
Implementation of a barcode on each item or product is assigned that provides the real date and update of the product such as SKU and serial number. Barcode makes the tracking system easier by tracking the product via its barcode and serial number.
- Accuracy and Speed:
Implementing a barcode system on products and items completely eliminates human error which also ensures capturing data in one go and keeping a record of the scanning products to make the workflow fast, such as packing, delivering, and shipping. It improves swift identification and tracking of items in inventory management reducing the storage space.
- Enhanced Inventory and Flexibility:
To enhance inventory management it is crucial to make use of a barcode system that gathers data and gives real updates of stockouts and overstocking. Providing correct and real-time information on products eliminates the risk of stockout items and overstocking of products which gathers huge space in a warehouse.
Different types of Barcode Used in a Warehouse:
QR Codes (Quick Response Codes)
The most popular yet effective QR codes are widely used in marketing, promotions, and mobile interactions. This QR code also known as a 2D barcode stores various types of data such as phone numbers, URL codes, and mobile interactions.
Linear Barcode: Also referred to as 1D barcode consists of parallel lines with different widths and spacing. They are often used for product identification, inventory management, and pricing. They encode data horizontally.
2D Barcodes:
In comparison to Linear barcodes, 2D barcodes are more efficient and have more potential because they have both horizontal and vertical patterns and hold huge data. They are widely used for applications widely use for more information such as URLs contact details, and product specifications.
Advantages of Barcode and RFID Technology:
- Enhanced Data Quality:
Eliminating data entry errors Barcode and RFID technology provide precise accurate inventory tracking and reduce discrepancies.
- Improved Efficiency:
The speed and accuracy provided by barcode and RFID increase the workflow and thus improve the entire operation.
- Real-Time Visibility:
These technologies provide real-time tracking of inventory delivering information on stock level information and movements. This technique helps optimize storage space in a warehouse such as facilitating order fulfillment and improving customer satisfaction by providing timely delivery.
- Improved Traceability:
To control the overall operation of the supply chain integration of barcode and RFID technology plays a huge role in this approach. Enabling efficient recall management and quality control.
Also Read: The Role of Technology in Cross-Docking
Final verdict:
Optimizing warehouse storage can provide various benefits to businesses such as reducing costs, increasing customer satisfaction, and achieving operational excellence. This article has explained the key strategies on how you can optimize your warehouse storage efficiently.
The main aspect of this article is to deliver insight information on how businesses can improve their inventory control while eliminating the regular errors in a warehouse.
Implementing advanced technologies while conducting regular assessments enabling proper tracking, shipping, and dispatching can achieve higher inventory accuracy in supply chain activities.
In addition, integrating the ABC method in a warehouse can reduce the storage space gathered by huge cartons. Integrating advanced technologies and key factors into a warehouse can give some great outcomes and maximize space utilization. Following the above-mentioned strategies warehouses can optimize their warehouse storage efficiently.
FAQs: How to Optimize Warehouse Storage for Efficiency
What does warehouse storage optimization entail, and why is it crucial for businesses?
Understand the concept of optimizing warehouse storage and its significance in enhancing overall operational efficiency.
What are the key factors to consider when designing a warehouse layout for optimal storage efficiency?
Explore the essential considerations in planning the layout of a warehouse to maximize storage capacity and streamline processes.
How can businesses determine the right storage systems or racking solutions for their specific needs?
Gain insights into the factors influencing the selection of storage systems and racking solutions tailored to the unique requirements of a business.
What role does inventory management play in warehouse storage optimization, and what best practices should be followed?
Learn about the impact of effective inventory management on storage optimization and discover best practices for maintaining accurate inventory levels.
Are there technologies available to assist in warehouse storage optimization, and how do they work?
Explore the technological solutions, such as Warehouse Management Systems (WMS) and automation, that contribute to optimizing warehouse storage processes.
How can businesses implement a system for efficient picking and packing within their warehouse?
Understand the strategies and methodologies for optimizing the picking and packing processes to improve overall warehouse efficiency.
What measures can be taken to maximize vertical storage space in a warehouse?
Discover techniques for utilizing vertical space efficiently, including the implementation of mezzanine floors and high-density storage solutions.
Are there industry-specific considerations for warehouse storage optimization, and how can businesses tailor their approach?
Learn about considerations specific to various industries and how businesses can customize their storage optimization strategies accordingly.
What role does employee training play in warehouse storage optimization, and how can staff efficiency be improved?
Explore the importance of training warehouse staff and implementing continuous improvement initiatives to enhance overall efficiency.
In the event of expanding or redesigning a warehouse, what steps should businesses take to ensure continued storage optimization?
Understand the steps involved in expanding or redesigning a warehouse to accommodate growth while maintaining or improving storage efficiency.