Table of Contents
Today, warehouses are the core of commerce and trade. In this advanced world, just in the blink of an eye, you order something and it reaches your doorstep in 48 hours or less.
But have you ever thought about the hands that pack, scan, and lift your deliveries daily facing several injuries? Warehouses can be dangerous if not heed proper precautions and safety measures.
Discussing warehouse safety standards and their importance will compel you to provide warehouse safety equipment and warehouse safety tips to your employees.
What is Warehouse
A warehouse is a center or a plain building that stores goods before delivering, such as preparing and packing before distribution which is usually done by manufacturers, wholesalers, customers, etc.
Or it is the system that keeps an eye on the checklist and updates about the availability of stock and the status of delivery of goods.
In other words, this system has a crucial part in supply chain management. It is a supply chain system that will always be up to date and only specific people have access to it according to warehouse safety rules.
Safety Procedures: Warehouse safety standards
Warehouse safety is a set of warehouse safety guidelines, warehouse safety rules, and precautions to ensure the safety of employees working in the warehouse.
Guidelines that are established by government agencies such as the United States Occupation Safety and Health Administration OSHA to reduce the risk of injuries and accidents for worker safety in warehouses.
Osha claims that the deadly harm rate in the warehouse is greater than the overall national average.
That is why they put more emphasis on protection and developed unique warehouse safety standards and warehouse safety protocols.
Importance of Safety in Warehouses
To be honest, a warehouse is a dangerous workplace to work in if proper safety is not considered.
Minor to lethal injuries in warehouses for warehouse workers are common which can sometimes lead to death.
So it is important to keep warehouse safety hazards in view and follow warehouse safety guidelines and rules to avoid future harm and risk of injury.
Bureau of Labor Statistics claims that in 2017 the total nonfatal injuries and illness in warehouses had over 24,000.
In addition to the risk of physical harm, a warehouse can be a dangerous place because of the presence of hazardous products.
Moreover, many dangerous chemicals, house chemicals, and other multiple-hazard products are stored in warehouses.
If not managed properly can seriously endanger the health of employees the importance of warehouse safety standards cannot be ignored.
Here is why.
Protect Lives and Health; The goal of warehouse safety standards is to safeguard the life and health of employees. With their lofty shelves, fast-moving machinery and heavy equipment warehouses can be inherently dangerous places.
In many countries implementing safety measures is not just morally imperative but also a legal obligation. The fundamental goal of these guidelines is to reduce the level of accidents and injuries.
Decreasing cost; In the warehouse injuries and accidents may cost a lot of money. For instance; medical bills, worker compensation claims, potential legal liability, and even damage to inventory.
By eliminating accidents and injuries the integrity of stored products warehouse safety guidelines play a significant role in minimizing these costs.
Improving efficiency;
Safety and efficiency aren’t meant to be mutually exclusive. In reality, safe warehouses tend to be more secure. Following the warehouse safety guidelines can reduce the level of accidents and equipment malfunctions, ensuring smooth operations.
Furthermore, a safe culture can boost worker morale leading to higher productivity.
Legal obligation; Noncompliance with safety regulations can lead to severe legal obligations including fines and business disruption. Staying up to date and following warehouse safety rules can eliminate such issues.
OSHA warehouse safety
Although OSHA does not have any specific laws or regulations several basic safety standards apply to warehouses such as;
Hazard Communication: Warehouse Safety Training
A formal hazard communication program needs to be prepared to implement an official Hazard Communication program. A safety rule for warehouse workers who are exposed to hazards and harsh chemicals. Should be aware of them and know how to protect themselves.
Emergency Action Plan (EAP): Improve Safety
This should be a mandatory step if the owner of the warehouse doesn’t have an in-house fire safety plan they should create one EAP.
In case of a sudden accident, EAP must contain evacuation instructions in case of fire or other emergency.
Exit Routes: Ensure Safety
A warehouse should have a well-built and well-constructed rescue exit. These exit routes should be marked and free of obstructions.
It should be located in a corner where there is no danger of exposure to toxic fumes or smoke.
First AID and Cardiopulmonary resuscitation (CPR)
Proper training in First Aid and CPR should be provided to workers. Secondly, a first Aid kit should be available in the warehouse in case of emergency
Lastly, OSHA instructs warehouse managers to provide complete training in CPR and First Aid to prepare workers in case of trouble.
OSHA warehouse Standards
When examining the safety of properties of the business, OSHA defines 10 requirements which are:
- Hazard Communication
- Electrical, wiring techniques
- Guarding base and wall openings and holes
- Electrical system design
- Exits
- Forklifts
- Lockout/Tagout
- Portable fire extinguishers
- Oxygen safety
- Mechanical energy transmission
Advanced strategies for warehouse safety; Safe Warehouse
We live in a fast-moving world where changes take place instantly. Advanced technologies have taken over the world and helped businesses grow each day.
Few advanced technological strategies can be used in a warehouse which can benefit warehousing and the workers working in it. Let’s discuss what are those.
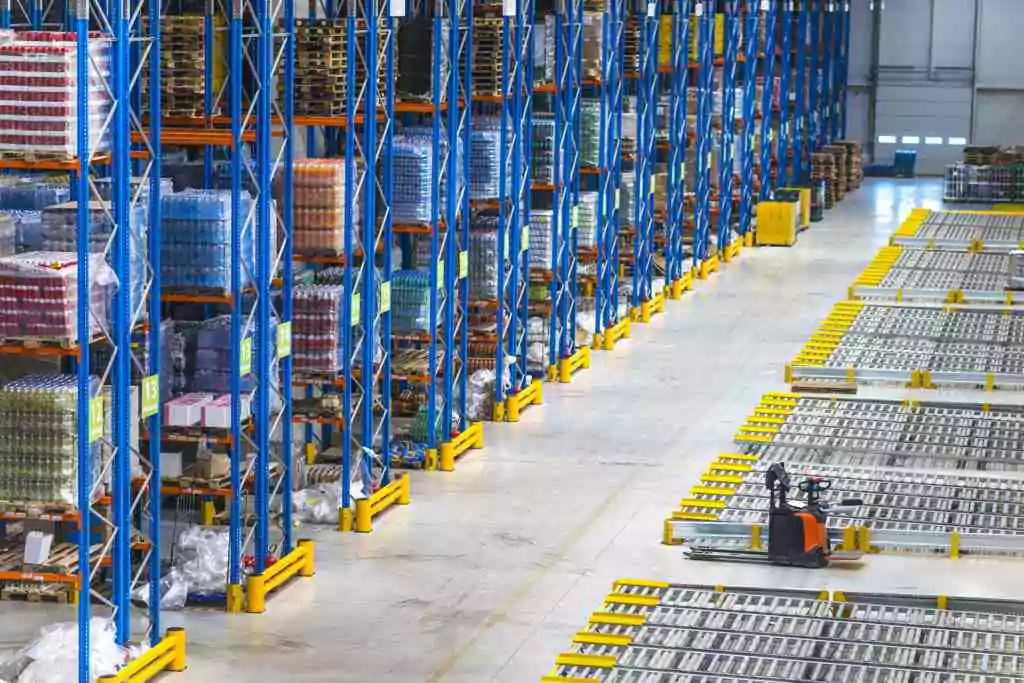
Safety audits and continuous improvement; Safety Inspections
Conduct a scheduled survey to spot the changes or threats that can be found in a warehouse and impose safety measures.
Address any issue on the dot to maintain a safe working environment.
Make your workers comfortable so that they can give honest feedback and thus, action can be taken for safety measures.
Important in a Warehouse: Reward and Recognition;
Impose an incentive program that rewards workers who follow safety standards and report safety concerns.
Staff may prioritize safety first in their everyday task if they get praise for their safe behavior.
Environmental consideration in a warehouse;
Prioritizing a safe and clean environment not only protects the environment but also contributes to overall safety.
Warehouse deals with multiple environmental factors which can be a little challenging for workers working there and the goods stored there.
Collision avoidance system;
In order to eliminate accidents involving pedestrians and other vehicles, install a collision avoidance system on forklifts.
Automated Guided Vehicles (AGVs)
Manual handling injuries are a common part of the warehouse to reduce the risk of human error, use AGVs to automate material handling tasks.
Safety Monitoring Software;
Install safety management software to track safety approaches, control safety inspections, and audits, and expedite incident reporting and investigation.
Managing and understanding these conditions is a crucial part of a warehouse, one knows how to tackle these inputs and the positive outcomes can be easily seen.
Some most common challenges and how to overcome them can be;
Temperature and Humidity;
Maintaining the ideal temperature for commodities stored there is one of the crucial parts of a warehouse particularly, for delicate products like electronics or food products.
Work comfort; warehouse temperature plays a huge role in a warehouse for employees employees safety is influenced by warehouse temperature.
In case of excessive heat or cold.
Proper lighting; adequate lighting is essential for employees for the safety of workers and identification of products.
Energy Efficiency; sustainability must strike the balance between natural energy and advanced lightning.
Air circulation; sufficient air ventilation reduces the likelihood of airborne pollutants and guarantees good air.
Dust and allergy management; managing dust and allergens items is crucial. Especially products that can generate airborne particles.
Noise pollution; working in a noise-free environment can be very comfortable for the staff in warehousing. maintaining a noise-free environment indeed can bring great outcomes.
Tight security; installing advanced surveillance systems that doesn’t allow unauthorized access in a warehouse.
Pest control; following preventive measures to protect foods and medicines is essential for stored goods.
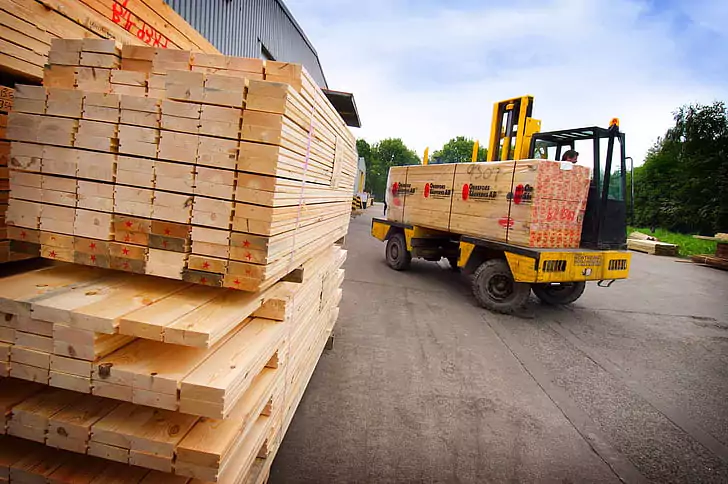
Also Read: About the Transloading Tactics
Warehouse safety equipment
OSHA orders all businesses to provide enough PPE (personal protective equipment)
To all warehouse workers. Those workers who are interested in completing an in-depth guide to PPE can consult OSHA`s personal protective equipment handbook.
Workers are instructed by OSHA to take continuous hazard assessments to figure out what forms of PPE are required. Every worker is eligible for it.
- PPE is provided to warehouse workers
- Assessment of proper care and use of ppe is provided
- Maintaining ppe in good order and replacing it when needed
Workers working in warehouses are not only responsible for using appropriate ppe. Workers must wear ppe correctly. For instance, attending sessions, clean and clear use of ppe, and notifying the supervisor when ppe needs to be replaced or repaired.
Several types of ppe used in warehouses are
- Safety helmets
- Gloves for protection
- Safety goggles or shades
- Steel-toed boots for fire safety
- Overall
- mandatory
Mandatory safety indications
Each warehouse is obliged to post warehouse safety signage. The warehouse signage guidelines guide employees on what type of signage is needed. Where and when it is needed, where exactly it should be placed, and how it should look like.
Safety guidelines in warehouses fall into several categories: general safety, fire safety, physical safety, admittance, and non-hazard.
Danger spots alert to the most serious of hazards.
Prohibited/warning signs show areas that could be dangerous but do not need as much caution as dangerous areas.
Lastly, Spots that are strictly prohibited, and signs highlighting areas that could cause minor injury or damage should not be avoided.
Ensuring a secure workplace; Warehouse safety tips
There are several tasks that warehouse workers complete, it is our duty to ensure and provide them a secure workplace. Some tips discussed below
Safety Training; life matters
Advance training should be provided to employees working in a warehouse. Advanced technology and warehouse safety guidelines should be introduced to minimize the hazard of injury or bodily harm.
In addition, this training should include how to identify and avoid possible hazards and training should be provided every 6 months for new or updated safety measures.
Proper equipment usage:
Maintain and inspect warehouse safety equipment, including forklifts, conveyors, and pallet jackets on a regular basis.
Keeping track of ongoing training of safe operations of usage of machinery and equipment.
Evident guidelines should be provided for storage and equipment use.
Material Handling:
Checklist of inventory to reduce the risk of future consequences.
Provide proper lifting equipment to lift products and to avoid bodily harm or injuries.
Heavy products should be stored at waist level to minimize the risk of injury during retrieval.
Usage of advanced equipment for material handling tasks.
Safety policies and procedures;
Mandatory policies and procedures should be introduced for warehouse employees. And should be reviewed on a daily basis.
Maintaining a neat and well-structured warehouse;
Whether it is a person’s life, home, or a warehouse a safe place is always safer. Employees should be encouraged to keep the workplace neat and clean for a safer environment.
Performing safety audits;
Because of unknown reasons the warehouse faces a lot of hazards, once the hazard is identified and corrected, a warehouse can function smoothly with less chance of damage.
Racking and storage;
Keeping daily checks and maintaining storage racks for solidity
Ensuring appropriate load ratings and guidelines for rack storage
Heavy items should be kept on a lower shelf to reduce injuries when lifting and lighter items on the lower self.
Personal Protective Equipment (PPE)
Ensure the proper use of personal protective equipment ppe such as safety helmets, goggles, steel-toed boots, helmets, and safety glasses.
Clean or replace ppe on a scheduled basis.
Security measures;
Control warehouse control restriction via keycard, and limited entrites.
Install secured cameras and alarm systems for security purposes to lessen the risk of theft and vandalism.
Conduct a background check of each person having access to limited locations.
Emergency Procedures;
Complete guidance in case of emergency, such as fire, accident, and medical emergencies.
Availability of fire extinguishers, first Aid kit, and eye wash solutions.
Conduct regular sessions to practice emergency measures.
Notifying and communicating about safety;
Encourage staff to notify if any occurrence emerges and report as soon as possible.
Keeping track of clear communication techniques for safety updates and notifications
and audits on a regular basis.
Remember people working for us matter and so their lives ensuring their safety will eventually build trust among each other and Hence, the sales will increase instantly.
Identifying warehouse safety hazards;
If we talk about any successful company, suppose the trending e-commerce business is at a peak because of its advanced strategies and planning with huge success, also faces huge losses as well.
However, keeping warehouse safety hazards in mind and correcting them before any damage can make a huge difference in one’s business.
There are some main safety hazards employees need to be aware of divided into few main categories.
- Physical hazards; Bodily harm
This hazard can cause bodily harm to workers working in a warehouse by lifting heavy racks and items. Which can cause severe injuries such as trips, slips, and falls, being knocked by an object, and being caught between or under an object.
- Chemical Hazards; injurious to health
These hazards can be quite serious to workers having Asthma and can cause severe health problems. If employees have such health concerns and if they are exposed to chemical hazards they can encounter irritated skin, respiratory irritants, and carcinogens.
- Ergonomic Hazards
These are the threats that can lead to musculoskeletal disorders such as redundant motion injuries and back injuries.
Workers who lift heavy loads without precaution can encounter such hazards
Some of the most everyday safety hazards in warehouses include.
- Slide, Trip, and Fall;
This is the most common challenge a worker encounters; a wet and oily base can cause a worker to slip and fall. This mainly happens when the floor is wet or oily. To prevent this from happening the floor should be clean and dry.
- Falling item;
Probably, objects that are kept on a higher shelf can easily fall on the workers working below.
To prevent this from happening heavy items should not be kept on huge racks instead they can be kept on the same height shelf so that they can easily be lifted.
- Electrical safety;
Make sure that all electricity installations and equipment meet standard rules and regulations.
Workers should be trained in electricity protocol if a sudden electricity threat comes up.
Knowledge of lockout/tagout and how to respond to electricity emergencies should be taught.
- Protection of vehicles and equipment;
Train workers on the safe operation of vehicles and equipment including forklifts and pallet jackets. To minimize the risk of accidents, develop traffic management strategies and impose vehicle maintenance schedules.
Warehouse Safety Rules and Guidelines;
Whether you are working in a hospital school or any organization, there are certain rules and guidelines for us to follow which are eventually for our own good.
There are some precautions warehouse workers need to follow and some guidelines to implement for themselves and their work.
Thus, a warehouse is an activity hub, numerous activities take place daily from the distribution of goods to companies to storing their goods while safety has been their top priority.
Today advanced warehouses require the safety of their staff and the protection of bailment of campanies.
Let’s delve into these beans and know how warehouse safety rules can be beneficial.
Advance Equipment Training;
An advanced warehouse deals with complex equipment and automation systems such as automated storage and AS/RS and robotic material handling.
To ensure the safety of such assets appoint expert operators and provide advanced training.
Only experienced or limited personnel should have the assets of such equipment.
Protocol for handling hazardous material;
Strict safety measures are required if your warehouse deals with dangerous materials. This involves rigorous adherence to appropriate dangerous substances handling and labeling.
Additionally, conduct regular emergency training drills to avoid future consequences.
Job Rotation and Ergonomics;
Implement ergonomics workstation assessment to combat the risk of musculoskeletal injuries.
Adjustable desks and appropriate gadgets should be used.
Job per-shift programs can also be implemented to mitigate repetitive strain by providing workers with multiple duties.
Radio frequency identifier RFID and inventory management;
RFID technology can be used for tracking which can increase productivity and safety.
The best component of this technology is that it reduces the requirement for manual intervention and improves inventory management.
It also eliminates the risk of workers climbing shelves or operating heavy machinery.
Advanced fire-safety protection;
Maximize fire safety by installing modern fire suppression equipment. This may alert early detection of fire, water mist, or inert gas suppression. These devices tend to be more effective in detecting and controlling flames while minimizing damage to stored material.
Autonomous Mobile Robots (AMRs)for cargo transport.
Incorporate Autonomous Mobile Robots (AMRs) To avoid accidents or mishaps, ensure safe integration with human workers, instruct employees, and guide them on how to use Autonomous Mobile Robots.
Data Analysis for continues Improvement;
Use data analysis to discover safety trends and patterns in advance. Near misses and incidents may be used to discover areas of improvement, update safety protocols, and invest resources where they are most required.
Training for emergency response drills;
Practice emergency response drills using accurate simulation. Scenarios that involve hazardous chemicals or complex automation systems should be included in these exercises.
The fundamental goal of this approach is to prepare workers for any emergency event.
Strategies for sustainability and the environment;
Use environmentally friendly techniques such as solar panels, rainwater harvesting, and waste reduction programs. By eliminating the carbon footprint and promoting eco-friendly practices among employees.
Committees for collaborative safety;
Establish a safety committee that consists of representatives from all departments and workers at every level. These groups can work together to identify safety concerns, find solutions, and foster a culture of safety throughout the business
Some advanced warehouse safety rules and regulations may include.
- Follow all rules and regulations mentioned in a safety outline to eliminate risk.
- It is mandatory to wear PPE when working in a warehouse
- If any emergency occurs, report as soon as possible to the supervisor.
- Keep the corridor, pathway, and desk clean and clutter-free.
- Use proper lifting techniques when lifting heavy machines to avoid injury.
- Use equipment and machinery only if properly trained and authorized.
- Do not block exit spots, fire extinguishers, or safety equipment.
- Take proper precautions and measure for handling hazardous material or chemical.
- Participate in safety training sessions and drills as required.
Implementing these warehouse safety rules and protocols can elevate warehouse safety to new heights.
Safety Communication in a warehouse;
Safety Conference; Regular safety meetings should be held to discuss safety topics, new updates, and safety procedures or guidelines and tackle employees’ safety concerns.
Safety marks; usage of proper emergency signage such as exit, hazardous spot, or designated pedestrian walkaways.
Safety Bulletin boards; these boards are for publishing safety information such as daily updates on safety measures, meeting updates, training schedules, and procedures to follow.
Walk-in policy; Make a comfortable environment where employees can get easy access to management to discuss safety concerns.
Safety feedback; worker viewpoints should be solicited and workers should be involved in the formulation and revision of safety rules and procedures.
Security metrics for warehouse;
Monitoring warehouse safety metrics may assist companies in tracking their old and new data such as tracking their performance in terms of safety, identifying trends, and making data-driven decisions to enhance safety.
Typical safety matrics include;
Total Recordable incident rate (TRIR)
The number of total incidents (injuries and illness) per 100 full-time workers warehousing during a certain period of time.
Lost Time Incident Rate (LTIR)
This incident rate resulted in lost work time per 100 full-time staff calculated over a specific period.
Close call report;
This means the number of near misses reported by employees can help find danger/hazards and prevent future incidents.
Findings from safety inspection;
The total number of risks found during safety inspection, as well as the results of efforts to tackle them.
Safety training completed session;
The number of employees enrolled in training and completed safety training.
Understanding and monitoring these safety metrics will guide businesses to have valuable insight into their performance and make efforts to reduce the risk of injuries and accidents.
Conclusion
Warehouse safety is a significant part of maintaining a productive and efficient work environment. By understanding warehouse safety standards warehouse safety rules and warehouse safety protocols, warehouse organisations can create a safe and secure environment for their employees. This comprehensive guide has provided you with information, knowledge, guidelines, and strategies that can increase the productivity of the warehouse.
Also Read: The Role of Technology in Cross-Docking
FAQS: warehouse safety standards
What are warehouse safety standards, and why are they important for businesses?
Understand the definition and significance of warehouse safety standards in ensuring a secure working environment.
What regulatory bodies or organizations set the standards for warehouse safety, and are they mandatory?
Identify the authorities or organizations responsible for establishing warehouse safety standards and whether compliance is obligatory.
What are the common types of safety hazards in warehouses, and how can they be mitigated?
Explore the various risks present in warehouse environments and effective strategies for minimizing or eliminating potential hazards.
How often should warehouse safety training be conducted, and what topics should it cover?
Learn about the frequency and key components of warehouse safety training programs to keep employees well-informed and prepared.
What safety measures should be in place for the handling of hazardous materials within a warehouse?
Understand the specific protocols and precautions required when dealing with hazardous materials in a warehouse setting.
How can technology be leveraged to enhance warehouse safety, and what innovative solutions are available?
Explore the role of technology, such as automation and sensor systems, in improving warehouse safety and accident prevention.
Are there specific requirements for the design and layout of a safe warehouse environment?
Gain insights into the optimal design principles for warehouses to promote safety, efficiency, and accessibility.
What should be included in a warehouse safety inspection checklist, and how often should inspections occur?
Access guidance on creating comprehensive safety checklists and establishing a routine inspection schedule to maintain safety standards.
What measures can warehouses take to ensure ergonomic safety and prevent workplace injuries?
Learn about ergonomic considerations and practices that contribute to employee well-being and reduce the risk of musculoskeletal issues.
In the event of an accident or emergency, what protocols and response plans should be in place?
Understand the importance of emergency preparedness and the steps to follow when responding to accidents, injuries, or unforeseen incidents in the warehouse.